CNC Lathe Factory: The Heart of Precision Engineering
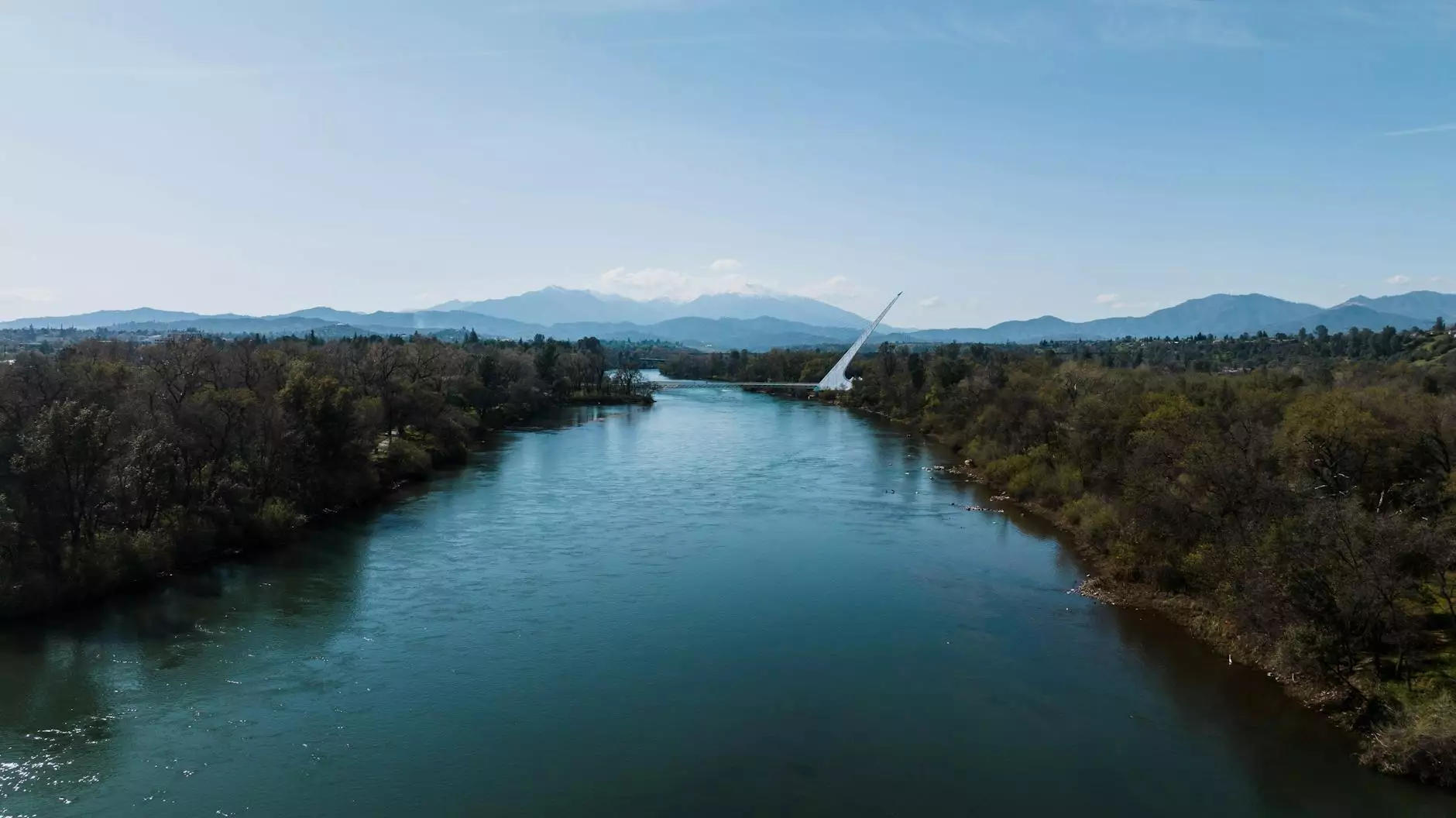
In an era where manufacturing is constantly evolving, the role of a cnc lathe factory has become indispensable. With the increasing demand for high-precision components across various industries, these factories have established themselves as pioneers of innovation and quality. This article delves into the intricacies of CNC lathe machining, its benefits, applications, and how it enhances productivity in the realm of metal fabrication.
Understanding CNC Lathes
CNC, or Computer Numerical Control, lathes are advanced machines that automate the lathe machining process, allowing for exceptional precision and consistency in producing intricate metal components. Traditional lathes, operated by skilled machinists, are being complemented and often replaced by CNC lathes due to their ability to produce complex shapes with minimal human intervention.
The Mechanism Behind CNC Lathes
In a cnc lathe factory, the operation begins with computer programming, where specific instructions define the shape, size, and dimensions of the parts to be produced. This programming controls the movement of the lathe and includes parameters like:
- Cutting speed: The velocity at which the cutting tool interacts with the workpiece.
- Feed rate: The distance the tool advances during each revolution of the lathe.
- Tool path: The trajectory that the machine follows while cutting the material.
Once programmed, the CNC lathe executes these instructions with unparalleled accuracy, resulting in parts that meet stringent specifications every time.
The Advantages of Using CNC Lathes
The rise of the cnc lathe factory model has transformed metal fabrication, yielding numerous benefits that contribute to efficiency and quality. Here are some key advantages:
1. Precision and Accuracy
CNC lathes can produce parts with tolerances as tight as ±0.001 inches. This high level of accuracy is essential in industries where exact specifications are paramount, such as aerospace, automotive, and medical device manufacturing.
2. Increased Production Speed
The automation of the lathe process enables faster production cycles. What used to take hours or days can now be accomplished in a fraction of the time as CNC lathes can operate continuously with minimal downtime.
3. Consistency in Quality
Human error is significantly reduced with CNC technology, leading to uniform quality across batches of products. This consistency ensures that each component adheres to the required standards, minimizing waste and rework.
4. Enhanced Flexibility
With the ability to quickly change programs and tool settings, CNC lathes offer unmatched flexibility. Manufacturers can easily shift from one product line to another with just a few adjustments, catering to market demands without incurring heavy retooling costs.
5. Cost Efficiency
While the initial investment in CNC technology can be substantial, the long-term savings in labor, materials, and overhead make it a financially sound choice for many manufacturers.
Applications of CNC Lathe Manufacturing
The versatility of CNC lathes allows them to be utilized in various sectors. Some common applications include:
- Aerospace Components: CNC lathes produce critical components such as turbine blades, gear housings, and brackets with high precision, essential for flight safety.
- Automotive Parts: From engine blocks to transmission components, CNC lathes manufacture automotive parts that require durability and performance.
- Medical Devices: Precision machined components such as surgical instruments or implants are produced to meet stringent health regulations.
- Electronics: The production of intricate housings and fittings for electronic components relies heavily on CNC machining for their complexity and detail.
Quality Control in CNC Lathe Factories
Quality control is a critical aspect of the manufacturing process in a cnc lathe factory. Ensuring that every product meets industry standards involves a series of rigorous checks and balances:
1. Incoming Material Inspection
The first step in quality control begins with the inspection of raw materials. Only high-grade materials that meet the required specifications are accepted for production.
2. In-Process Monitoring
Throughout the machining process, various parameters such as temperature, cutting speed, and vibration are monitored to ensure that they remain within acceptable limits. This real-time feedback allows for immediate adjustments.
3. Final Inspection
After production, components are measured using precise measuring instruments like calipers and coordinate measuring machines (CMMs) to verify that they match the specifications.
The Future of CNC Lathe Factories
The landscape of CNC lathe manufacturing is continually evolving, with new technologies and techniques emerging to enhance the efficiency and capability of these machines. Some trends to watch include:
1. Integration of AI and Machine Learning
Artificial Intelligence (AI) is being integrated into CNC systems to enable predictive maintenance, process optimization, and even autonomous machining operations, further improving efficiency.
2. The Use of Advanced Materials
With the continued development of advanced materials such as composites and alloys, CNC lathes are being adapted to process these materials effectively, broadening their application range.
3. Sustainable Practices
As industries aim to reduce their environmental impact, CNC lathe factories are exploring sustainable practices like energy-efficient machinery, recycling scrap materials, and reducing waste through optimized machining strategies.
Conclusion
In conclusion, the cnc lathe factory is a cornerstone of modern metal fabrication. Its ability to produce high-precision components quickly and consistently addresses the evolving needs of industries across the globe. With advancements in technology and a commitment to quality, CNC lathe factories continue to push the boundaries of what is possible in manufacturing. As we move further into a tech-driven future, it is clear that these factories will play an essential role in shaping the next era of manufacturing excellence.