Unlocking Efficiency: The Essential Role of Lubrication Fittings
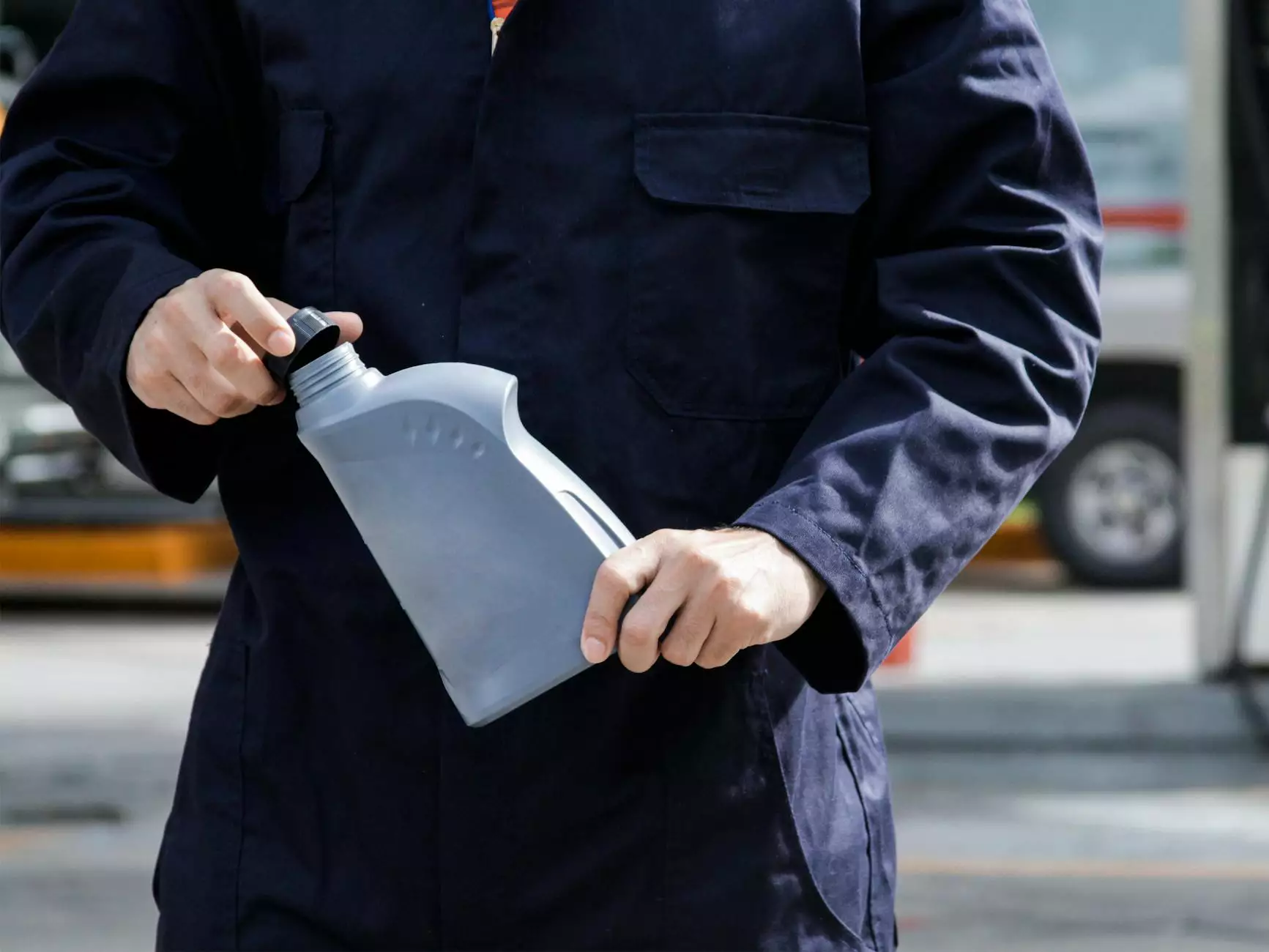
In today's competitive business environment, maintaining the efficiency and longevity of your machinery is paramount. One often overlooked but critical component in this equation is lubrication fittings. These small yet mighty fittings play a vital role in ensuring that your equipment runs smoothly and operates at peak performance.
Understanding Lubrication Fittings
Lubrication fittings, also known as grease fittings or zerks, are designed to facilitate the application of lubricant to machinery. They are typically found on various types of equipment, including industrial machinery, automotive components, and even household appliances. Their primary function is to allow for easy and controlled application of grease or oil, ensuring that moving parts receive the necessary lubrication to prevent excessive wear and tear.
Types of Lubrication Fittings
There are several types of lubrication fittings, each tailored to specific applications. Understanding these types can help you choose the right fitting for your machinery:
- Zerk Fittings: The most common type, allowing for easy attachment of a grease gun.
- Flat Lubrication Fittings: Used in applications where space is tight; they can be installed flush with the surface.
- Threaded Lubrication Fittings: Featuring a male or female thread, these fittings provide a secure connection with grease guns.
- Push-On Fittings: These fittings are quickly engaged and disengaged, making them ideal for frequent lubrication points.
The Importance of Lubrication in Machinery
Lubrication is essential to the smooth operation of machinery. The benefits of regular lubrication include:
- Reduced Friction: Proper lubrication minimizes friction between moving parts, which can lead to overheating and damage.
- Prevention of Corrosion: Lubricants can help to repel moisture and contaminants, protecting the metal surfaces of your equipment.
- Increased Efficiency: Well-lubricated machinery operates more efficiently, consuming less energy and requiring less frequent maintenance.
- Extended Lifespan: Regular lubrication leads to less wear on components, extending their usable life and reducing replacement costs.
How to Choose the Right Lubrication Fittings
Selecting the right lubrication fittings is crucial for ensuring that your equipment is properly maintained. Here are several factors to consider:
- Application Type: Identify the specific machinery and the type of lubricant required.
- Environmental Conditions: Consider where the machinery is operating; high humidity or heat may influence your choice.
- Space Constraints: Choose fittings that fit within the available space and offer ease of access for lubrication tasks.
- Durability: Select fittings made from robust materials that can withstand the rigors of the operating environment.
Best Practices for Using Lubrication Fittings
To maximize the effectiveness of your lubrication fittings, adhere to these best practices:
- Regular Inspection: Frequently check lubrication fittings for signs of wear or damage.
- Follow Manufacturer Recommendations: Always use the specified lubricant type and follow recommended lubrication intervals.
- Proper Application Techniques: Use the correct pressure when applying lubricant to prevent damage to seals or fittings.
- Keep Fittings Clean: Ensure that the area around the fitting is kept clean to avoid contaminating the lubricant.
Benefits of Investing in High-Quality Lubrication Fittings
Investing in high-quality lubrication fittings can yield significant returns for your business. Some key benefits include:
- Enhanced Reliability: Quality fittings ensure a reliable connection for lubrication, reducing the chances of equipment failure.
- Cost Savings: By extending the lifespan of your machinery through proper lubrication, you can save on downtime and repairs.
- Improved Safety: Well-maintained equipment is less likely to malfunction, reducing the risk of workplace accidents.
- Better Performance: With optimal lubrication, machinery performs better, leading to increased productivity.
Common Mistakes to Avoid with Lubrication Fittings
To ensure your fittings serve their purpose effectively, avoid these common mistakes:
- Over-lubricating: This can lead to excess pressure on seals and grease escaping from the fittings.
- Ignoring Signs of Wear: Regularly inspect and replace worn or damaged fittings to prevent issues before they escalate.
- Using Incorrect Lubricants: Always use the lubricant type recommended by the manufacturer for optimal performance.
Where to Buy Quality Lubrication Fittings
When it comes to purchasing lubrication fittings, quality should always be a priority. Here are some tips for finding reputable suppliers:
- Research Suppliers: Look for companies with a strong reputation in the industry and positive customer reviews.
- Check Certifications: Ensure that the supplier's products meet industry standards and certifications for quality.
- Consider Custom Solutions: Some suppliers may offer customized fitting solutions tailored to specific machinery needs.
- Purchase in Bulk: If you manage an extensive fleet or multiple machines, consider bulk purchasing to save money.
The Future of Lubrication Fittings
As technology continues to evolve, so does the future of lubrication fittings. Innovations in materials and design are leading to more efficient and durable fittings that can withstand harsher conditions and deliver precise lubrication. Smart lubrication systems that monitor and automate the lubrication process are also gaining traction, further enhancing machinery maintenance and operational efficiency.
Final Thoughts
The role of lubrication fittings in machinery maintenance cannot be overstated. By investing time and resources into understanding and implementing proper lubrication practices, businesses can ensure their equipment remains in optimal condition, thus enhancing productivity and profitability.
For those looking for high-quality fittings, consider visiting fitsch.cn, where you'll find a comprehensive selection of fittings designed to meet any lubrication requirement.